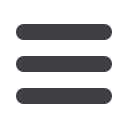
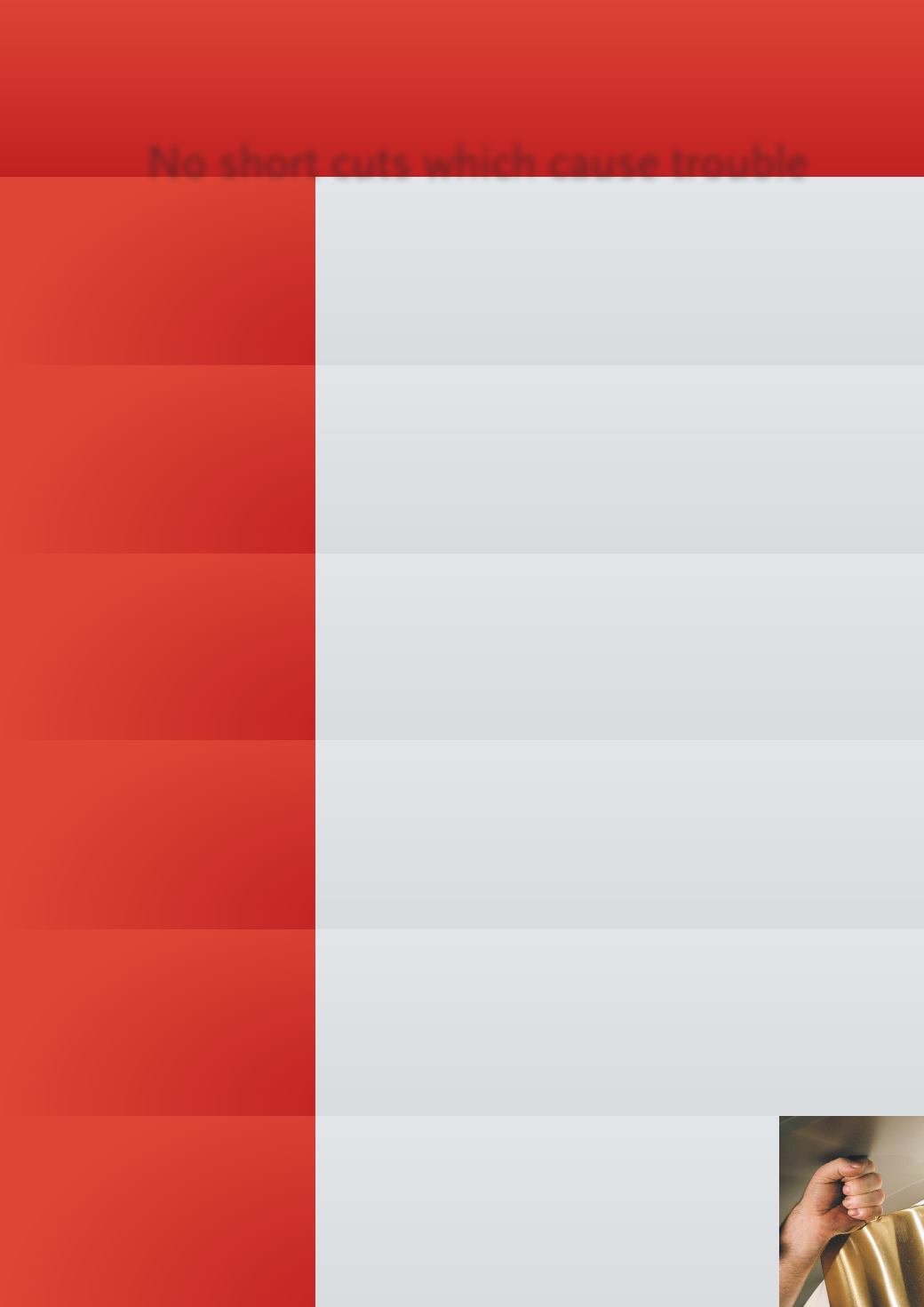
No short cuts which cause trouble
Inadequate
sealing
systems
– may allow seawater to enter the thruster – the most
frequent cause of thruster failure.
Seawater in the oil can destroy gears, bearings and other
vital components inside the unit.
Overpowering
– for example by stretching the length of the gear teeth –
causes overloading of the gear.
This shortens the lifetime and increases maintenance costs.
If a tooth actually breaks, costly repairs will be needed.
Overspeeding
– results in excessive propeller cavitation, thrust loss and
heavy erosion of the propeller blades and the walls of the
tunnel.
Thismay in turn increase wear and tear as well as life cycle costs.
Reducing the
structural
rigidity
– normally means a less robust design that cuts safety margins.
Inadequate structural rigidity results in vibration that can
cause serious damage both to the thruster and to other
equipment in the thruster room.
Excessive
propeller tip
clearance
Some thrusters have a large clearance
between the blade and the tunnel to allow for
imprecision and distortion during installation
– downgrading the performance.
Stripping
essential
features
– such as the rope guard – exposes the propeller shaft
sealing system to damage from debris.
Without a rope guard, shipowners must consider other
means of protection.